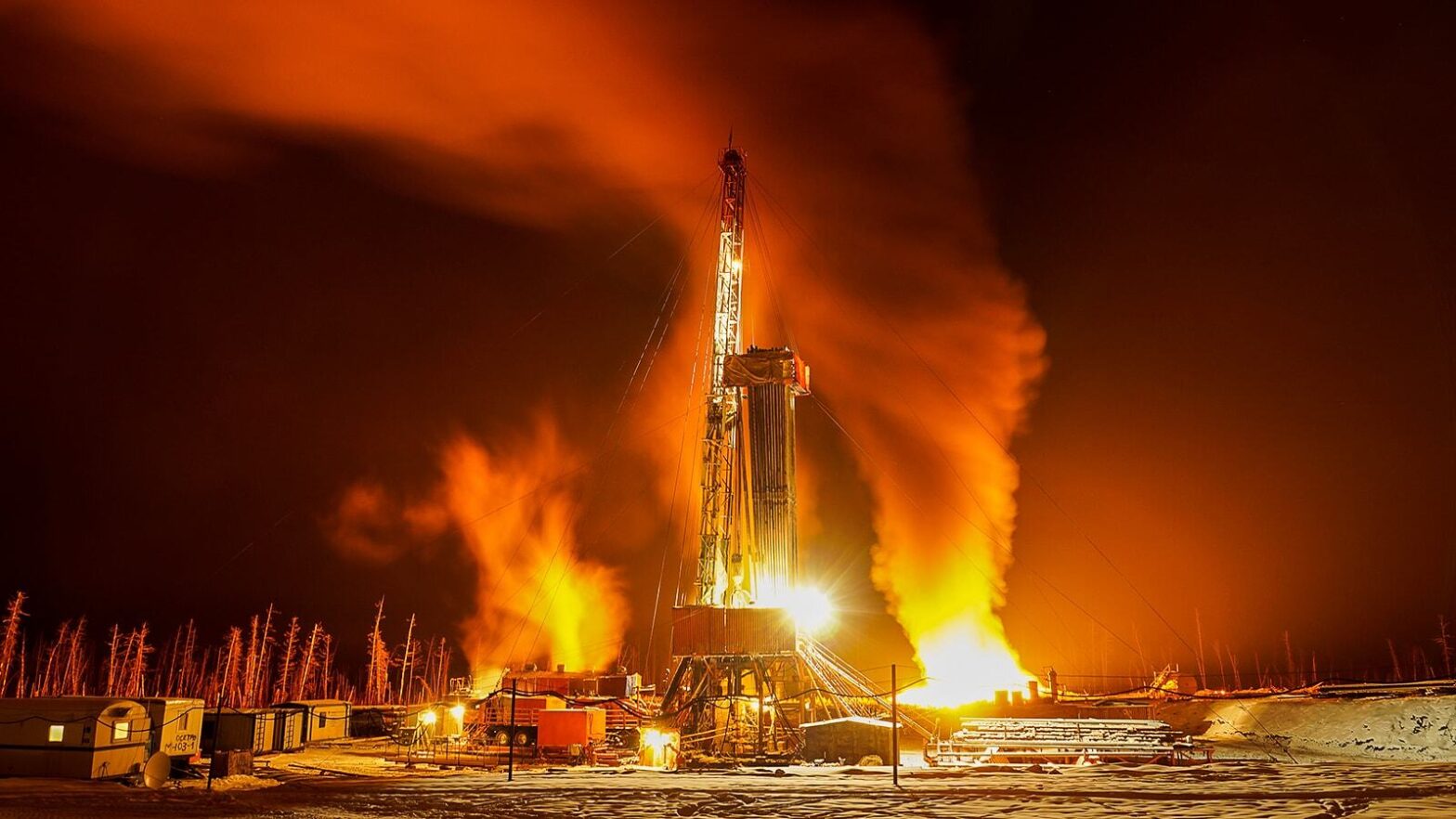
NSF awards $6.6M for two highly collaborative projects aimed at a more sustainable future
By
on
The projects include faculty from across chemical and biological engineering and mechanical and aerospace engineering. The projects feature highly collaborative teams working across a range of disciplines to address a systemic set of environmental problems from the ground up.
Better Living through Plasma
A team led by Michele Sarazen, assistant professor of chemical and biological engineering, will develop a more effective way to produce liquid fuel from methane, a gas emitted as pollution from oil fields and other sites around the world. The new system would save both energy and money, and reduce hazardous emissions. The NSF awarded the project $2M over four years.
“The idea is to think of a process that is currently done only at the large scale, in certain locations, and try to transform it into a technology that is run at the small scale,” said Sarazen, the project’s principal investigator. “You can locally create the chemical or the fuel that you’re making and have it available at the site where you need to use it, as opposed to making it at one place and then distributing it across the country or across the world.”
Currently, large, centralized reactors refine shale gas (methane) and petroleum into liquid fuel and chemicals. These facilities require massive amounts of heat input to activate the necessary chemistry and a vast transportation network to move both the raw material and the refined product around the country. The Sarazen-led team seeks to create smaller, more efficient reactors that could be widely distributed for a more localized network, potentially including onsite at oil reservoirs, where methane gas is vented and burned off as waste. The project represents a dramatic re-envisioning and streamlining of natural gas utilization.
Their proposed system takes advantage of two key elements: 3D printing technology that allows for relatively cheap precision manufacturing, and the development of technology known as misty plasma catalysis, which combines microscopic water particles with novel plasma catalysts to greatly reduce the heat and energy required for natural gas conversion to fuels and chemicals. Because the project envisions distributing the processing network across many sites, the system would reduce the impacts of transporting both the raw materials and the end fuel product, further cutting the greenhouse gas emissions associated with natural gas.
The team includes Yiguang Ju, Robert Porter Patterson Professor of Mechanical and Aerospace Engineering at Princeton; Xiaolin Zheng, of Stanford University; and Tanvir Farouk and Lang Yuan, both of the University of South Carolina at Columbia.
Towards Sustainable Future Manufacturing
A collaborative team of researchers will re-imagine the future of manufacturing by drawing from nature to design lightweight, durable materials for construction. The key to their approach lies in combining a wide range of disciplines to bridge the gaps between the very small and the very large, according to Pierre-Thomas Brun, an assistant professor of chemical and biological engineering.
One goal of the project is to re-engineer one of the most wasteful and common elements of construction: pouring concrete. Current methods involve erecting large scaffolds of wood and other materials that are thrown away after their brief use. Instead, the researchers plan to develop self-morphing building blocks – starting from nanoscale particles and assembling to macroscale objects – which will be used to construct lightweight origami-like structures that transform from flat sheets into the specific structures needed and can be re-used. Similar techniques also are expected to improve cooling and noise protection in sustainable building materials.
The NSF funded project will receive $4.6 million over five years, split between the project’s five groups, including those led by Brun and Andrei Košmrlj, an assistant professor of mechanical and aerospace engineering.
The team consists of experts in architecture, mechanics, fluid dynamics, and 3D printing, as well as researchers in materials science, chemistry, and biophysics, who study materials that mimic biological structures like trees, silk webs and dragonfly wings.
“To be functional, natural materials rely on their structure and architecture rather than their chemistry alone,” Brun said. “They outperform many of the materials that we’re manufacturing today. And clearly they have a lower carbon footprint and they are more sustainable by design.”
But creating composite materials that mimic these ultra-durable, environmentally sustainable natural designs requires comprehending a vast number of highly intricate hierarchical patterns across scales. The team will synthesize biopolymer composites on the nano- and microscale by exploiting the self-assembly and phase separation, which will be guided by mathematical models recently developed by Košmrlj to achieve desired morphology.
Brun, bringing his expertise in additive manufacturing, or 3D printing, will lead the push to link the microscale to the macroscale. Brun will develop a way to direct the assembly of those microscale building blocks — effectively printing them with a biomimetic ink — into the repeating patterns set forth by the structural team. The biomimetic inks printed by Brun will swell/shrink in response external stimuli and they will serve as actuators for the origami and kirigami-like structures. Košmrlj, using advanced computational methods, will draw on the Japanese art forms of origami and kirigami to reverse engineer complex folding patterns, essential for scaling these printed structures into large, durable architectural designs.
“There are many examples of such morphable origami and kirigami structures on the centimeter scale, but none of the current approaches can be translated to the macroscale because the materials used in these applications are not strong enough to sustain gravitational loads,” Košmrlj said. He added that the sustainable materials this team plans to design “will have a very high strength and they will be able to be repurposed, reused and recycled.”
Their project is one of 27 nationwide funded through a competitive grant-making process around the future of manufacturing. “Our investment provides industry with manufacturing tools that currently live only in the laboratory, or the imagination,” said NSF Director Sethuraman Panchanathan. “Through the convergence of such fields as robotics, artificial intelligence, biotechnology and materials research, future manufacturing will create revolutionary products with unprecedented capabilities, produced sustainably in facilities across the country by a diverse, newly trained workforce.”
The project’s principal investigator Shu Yang, from the University of Pennsylvania, and David Salas de la Cruz, of Rutgers University, will focus on synthesizing the molecules that provide the project’s foundation. The architect Masoud Akbarzadeh, also from Penn, will develop 3D models for the forms.