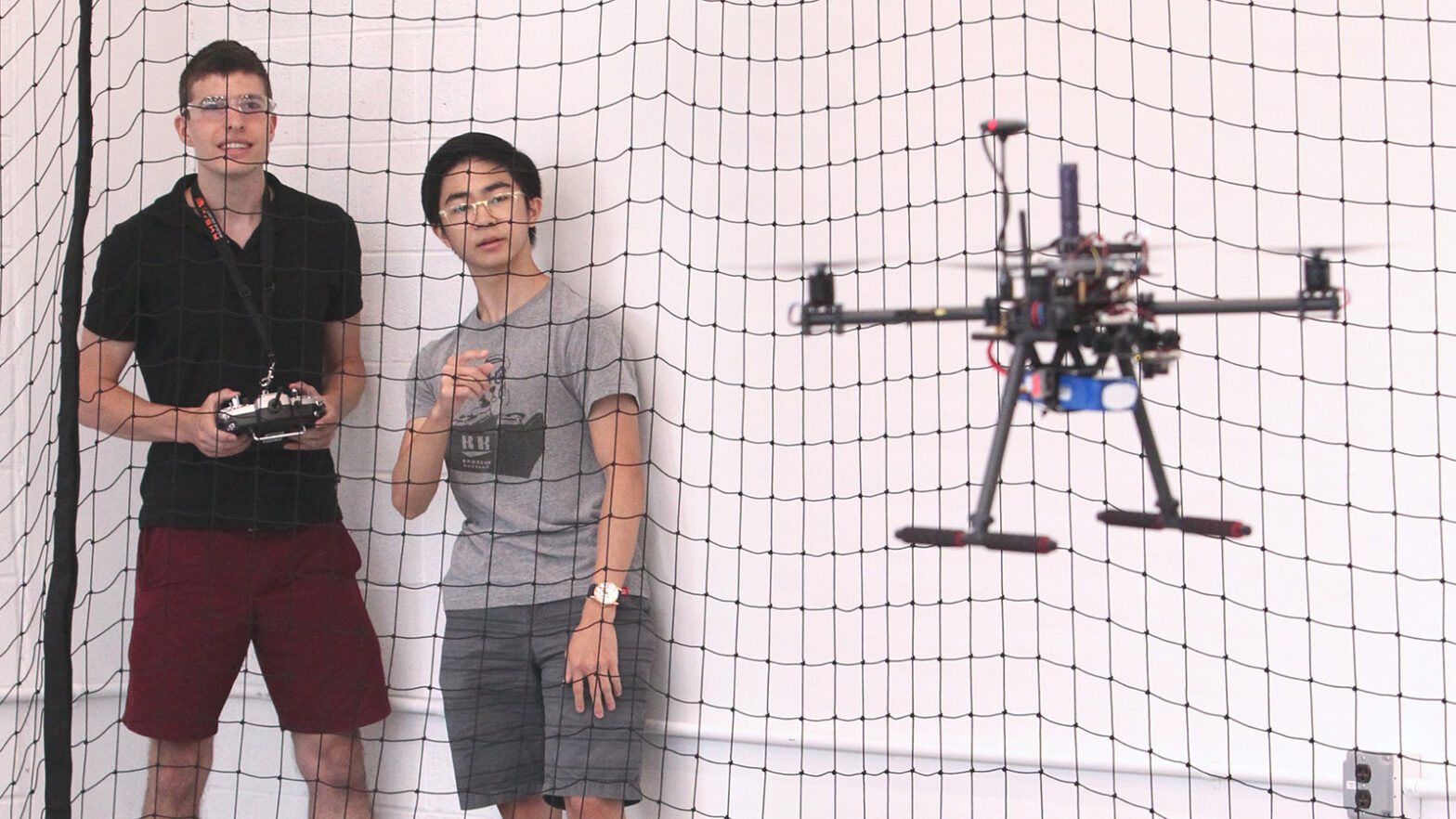
Small, efficient sensors help drones fly in high winds
But the expanded use of these unmanned aerial vehicles (UAVs) has been hampered in part by an inability to handle high winds or complex airflows around buildings.
Now, two Princeton engineers have teamed up to help drones fly better in gusts and gales. Anirudha Majumdar, an assistant professor of mechanical and aerospace engineering, focuses on safety and performance guarantees for robotic control systems, while Marcus Hultmark, associate professor in the same department, specializes in fluid mechanics.
Hultmark’s group has developed a new type of flow sensor — a micro-electromechanical system that uses a nanoscale conductive wire to measure humidity, temperature, or velocity with high speed and sensitivity.
Drones currently gauge airflow using downward-facing cameras or pitot tubes, which use a fluid pressure measurement. State-of-the-art drones can fly well at wind speeds of up to 20 miles per hour (like a typical windy day at the beach), but falter in stronger winds or shifting conditions, said Majumdar.
With an innovation grant from the engineering school’s Project X Fund, Majumdar and Hultmark are integrating their microsensors with a commercially available quadrotor drone. They aim to achieve safe, autonomous flight amid obstacles, with wind gusts of 40 to 50 miles per hour.
“For pilots, wind is a huge factor — it’s an invisible, often unpredictable force. This is especially true for flight near obstacles, like drone infrastructure inspections. To give drones the ability to sense and react to changes in the airflow would be gamechanging,” said Nathaniel Simon, who is leading the work as a Ph.D. student coadvised by Majumdar and Hultmark. Simon has piloted small planes since age 13.
Also contributing to the project is Kyle Ikuma, a junior in the mechanical and aerospace engineering department, who has been a drone hobbyist since eighth grade. “For me, it was always more fun building the drones than flying them,” said Ikuma. “That’s how I learned about 3D printing and how to use [computer-aided design software]” — valuable skills in his collaboration with Simon as part of the department’s Summer Practical Research Experience program.
Along with testing the microsensor-equipped drone in a wind tunnel, the researchers are developing new airflow models and simulations to optimize placement of the sensors and integrate airflow data with autonomous control algorithms.