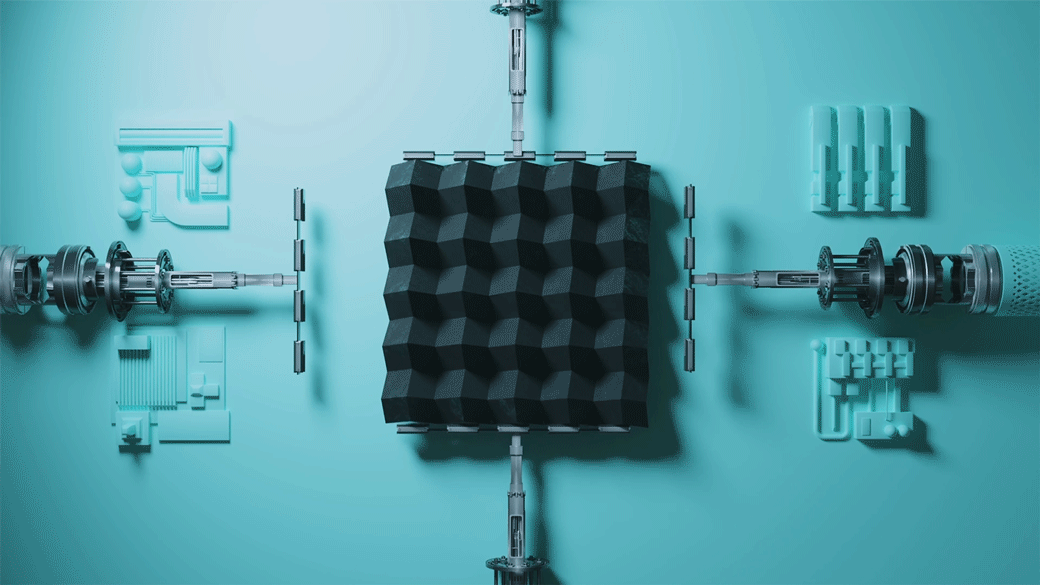
These engineers drew inspiration from geometrical frustration
Now, researchers have drawn inspiration from the art of origami to create programmable surfaces that allow engineers to alter physical properties of a uniform substance across a range of directions. In an article published in the Oct. 26 issue of the journal Advanced Materials, the researchers described structures that are also programmable, so dimensions and corresponding properties can shift as needed. The researchers hope that designers will be able to apply the techniques to medical devices, architecture, robotics and aerospace.
“We have an almost infinite number of adjustments, which provide a rich design space,” said Glaucio Paulino, the Margareta Engman Augustine Professor of Engineering and one of the principal researchers. Paulino, a professor of civil and environmental engineering and the Princeton Institute for the Science and Technology of Materials, worked with colleagues from the Indian Institute of Technology Madras, Peking University, the University of Tokyo and the University of Trento on the project.
To create the structures, the researchers began with cells of four kite-shaped figures known as rhombuses; each rhombus is connected to two others along two sides, with a tail end of each rhombus free. The connecting sides are hinged in some special ways, so each cell can click through a variety of forms, from a wide basket to thin folds. (See the corresponding video for more information.) The researchers combine many of these cells to create a wide range of surfaces.
By adjusting cells, the researchers can change the properties of the entire surface: Among the options, they can vary compressibility, flexibility and density. Because individual cells are adjustable, the researchers can vary properties within the surface and can easily change and adjust the properties.
“Usually, a single origami pattern has one specific mechanical property,” said Tomohiro Tachi, one of the researchers and a professor at the University of Tokyo. “This structure can switch between multiple states that have distinct properties. It is a universal module for programming and reprogramming materials with versatile properties.”
Each cell demonstrates three stable states, meaning they will hold the position once clicked into it. This feature is useful for engineers seeking to use the origami patterns in applications because it allows for greater control of structures. It also allows designers to use the techniques without needing to add supports for the structures as their orientation changes. For example, a designer could adjust a series of cells to make a surface more flexible in one area and be confident that the cells would hold this position without requiring additional support.
“What we observed experimentally is a real tri-stable structure because the stable states can be determined by the ‘click’ sound it emits when it snaps among the different configurations,” said Diego Misseroni, a professor at the University of Trento and a member of the research team.
The technique takes advantage of a phenomenon that physicists call frustration. In geometry, frustration is a feature that stops a pattern from propagating across a wide space — like a jagged rock in a snowfield. With the adjustable cells, the researchers can introduce frustration into structures. They use this to change the properties of the surface. They can do so over wide areas and small spots.
“A frustration is a kind of engineered defect, a defect by design,” Paulino said. “If a defect is arbitrary, it is usually bad. But if we can engineer it, we can use it in a way that is interesting.”
Co-researcher Ke Liu said he was pleased by the ability to turn a defect into an engineering advantage.
“A defect by design is no longer a defective flaw,” said Liu, a professor at Peking University. “In this work, we use the magic of origami to create a material whose defects can be programmed through geometric frustration.”
The researchers can use these engineered frustrations to precisely change the patterns of the surface. By changing the patterns, they can adjust the surface’s properties.
“A frustration line changes the density, or the alignment, or the composition of the material. This changes the material’s properties, and we can take advantage of that,” Paulino said.
Paulino said the researchers have used modeling and experimentation to demonstrate the use of the technique in one-dimensional and two-dimensional systems. He said the researchers are conducting further work to see how the technique works in three dimensions by stacking the cells as well as connecting them horizontally.
The inspiration for the technique came from crystallography, Paulino said. Many important material properties are determined by the geometry of crystalline structures. Diamonds’ clarity and strength, for example, depend on regular configurations of carbon structures. Paulino and his colleagues wanted to explore whether they could use geometry to mimic those conditions in larger-scale materials.
Phanisri Pratapa, one of the researchers and a professor at the Indian Institute of Technology Madras, said the researchers were encouraged by the results and eager to continue along this line of inquiry.
“The intriguing mechanisms exhibited by our folding material indicate the existence of more such mysteries in origami-based architected metamaterials that are yet to be unraveled,” he said.
The article, Triclinic metamaterials by tristable origami with reprogrammable frustration, was published Oct. 26 in the journal Advanced Materials with a front cover illustration. Support for the work was provided in part by the U.S. National Science Foundation, the Peking University College of Engineering, the Indian Department of Science & Technology, the European Commission, and the Japan Science and Technology Agency.