Giving a second life to construction materials after demolition, engineers at the University of São Paulo and Princeton have developed an approach for recycling cement waste into a sustainable, low-carbon alternative that is comparable in performance to the industry standard.
In addition to lowering the carbon intensity of the cement and concrete industry, the process could enable new uses for construction and demolition waste, of which concrete is a significant component. In 2018 in the United States, the total amount of construction and demolition waste was more than twice that of household waste.
“Construction waste typically ends up either in a landfill, or, if it’s recycled, will be used in low-grade applications such as in pavements or in soils,” said research leader Sérgio Angulo, a professor of Civil and Urban Construction Engineering at the University of São Paulo. “It’s exciting to show that we can, in fact, recycle this recovered cement waste into a high-quality application.”
In their paper, published in ACS Sustainable Chemistry & Engineering, the researchers demonstrated that mixtures containing up to 80% of this recycled cement were just as strong as conventional Portland cement by itself while generating a fraction of the carbon emissions. Portland cement is the most common binder used to create concrete, but its high carbon intensity is the main reason the cement and concrete industry is responsible for around 8% of global emissions.
If fully realized and deployed in coordination with other emerging technologies that replace cement, the researchers estimated that emissions from the cement industry could be cut by up to 61%. The estimated reductions blow past the 9% emissions cuts that the Global Cement and Concrete Association projected to be possible with so-called clinker replacement approaches.
“The leap forward here is that you can now get short- and long-term properties that are essentially the same as Portland cement by itself with a low-carbon alternative overwhelmingly composed of recycled materials,” said co-author Claire White, a professor of civil and environmental engineering and the Andlinger Center for Energy and the Environment.
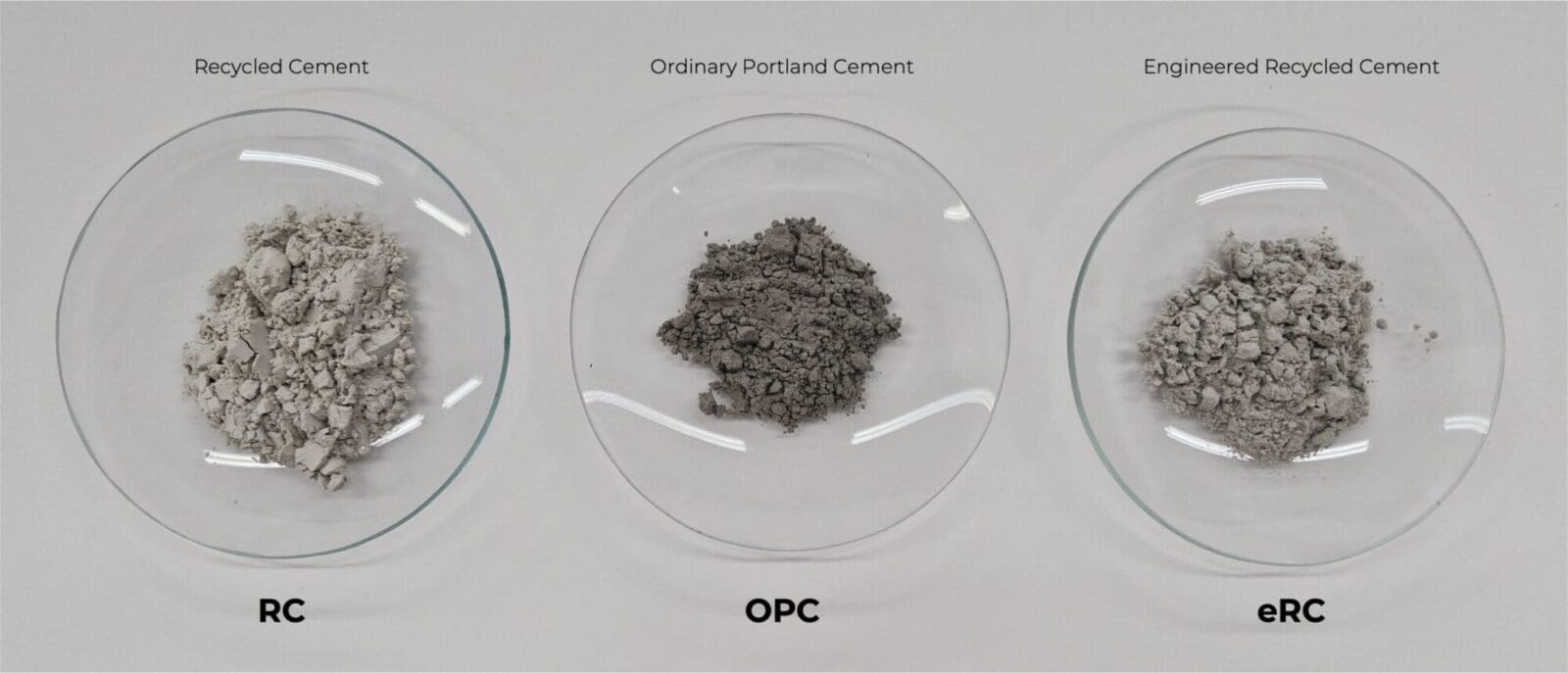
Enabling circular cements
At the core of the recycling approach is heat.
After pulverizing or crushing concrete into a fine powder — the researchers estimated that of the five gigatons of concrete waste produced annually, around one gigaton of this powder could be recovered by the industry — the team heated it to 500 °C. This temperature was high enough to dehydrate the cement powder and restore its properties as a binder but low enough to prevent the decomposition of carbonate components in the material, which would lead to additional carbon dioxide emissions.
While this ‘thermoactivated’ cement could be used on its own to make concrete, the researchers found that its high surface area and water demand during the mixing process led to a final material with high porosity and diminished strength. But by combining the recycled cement with small amounts of finely ground Portland cement or limestone, the resulting cement binder demonstrated strength gains and workability on par with industry standards.
The strength gain occurs because the finely ground Portland cement or limestone fills the pores in the recycled cement with a material other than water, reducing the overall water demand and even forming new products after the mixing process, called hydration products, that increase the material’s strength.
“Previously, if you only used thermoactivated recycled cement, it didn’t perform well enough to be an acceptable replacement,” White said. “But by lowering the surface area and optimizing the packing of particles in the material’s microstructure, we get something that behaves quite comparably to Portland cement.”
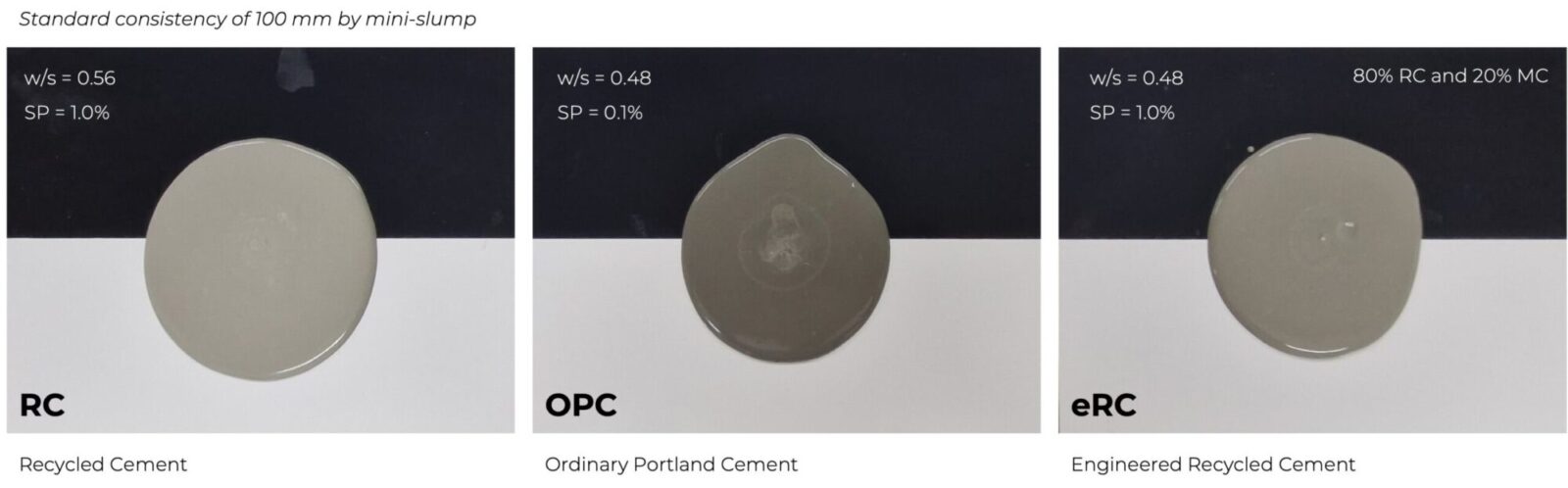
Since the process repurposes construction waste, the researchers said the process could move the world toward a more circular carbon economy while generating fewer carbon emissions than other emerging low-carbon cement alternatives. In the paper, for instance, the team estimates their cement emits between 198 to 320 kilograms of carbon dioxide per metric ton, up to 40% fewer emissions than a commercially available low-carbon alternative known as limestone calcined clay cement (LC3).
“With this technology, you could imagine cities becoming much more circular than today,” Angulo said. “Materials from demolished infrastructure can be directly used in new building projects.”
Despite such benefits, Angulo and White noted several technological, economic, and policy hurdles to the technology’s wide-scale deployment.
For instance, they explained that scaling the recycled cement would require a better approach for sorting and processing demolition waste, one that considers circularity rather than the landfill. The technology would also be most practical in mature cities with a reliable supply of aging building stock instead of rapidly developing areas with primarily new buildings.
Lastly, building codes developed when Portland cement was the dominant binder for concrete production would need to be updated, moving away from ‘recipe-based’ standards that specify certain cement compositions to ones that instead focus on performance-based requirements. Angulo said that several countries in Europe and Latin America have already begun to adopt such performance-based standards, which could permit the use of not just the recycled cements he studies but also a wide array of low-carbon alternatives.
“In Brazil, we are already beginning to implement performance-based standards for non-structural building envelopes and floors,” said Angulo. “Updating construction codes is important for allowing innovation in the building sector.”
Laying the foundations for an ongoing collaboration
The work on recycled cements results from a collaboration formed when Angulo came to Princeton as a visiting researcher in White’s group for a year, beginning in 2023.
Both researchers said that the collaboration — which has been ongoing even after Angulo’s return to Brazil — unlocked new research capabilities and perspectives that have improved their groups’ work.
For Angulo, tapping into White’s expertise in characterization techniques such as total X-ray scattering has helped him to better understand the driving mechanisms behind the materials he studies. For example, White and Angulo performed experiments during Angulo’s visit that will help them better understand how the atomic structure of the material changes as it undergoes thermal activation. This will help them answer questions about the durability of the recycled cement over multiple cycles of use and whether it is truly a ‘circular’ material.
For White, the collaboration allowed her to work on a class of cements that she had previously never studied, despite her extensive background in low-carbon concrete. Even beyond the recycled cement project, White said that Angulo’s visit provided her group with a totally new perspective on many of their projects, even those that appear far-removed from the world of recycled cements.
“This collaboration has had benefits in both directions,” White said. “Sergio’s brought his domain knowledge, my group has brought our expertise in advanced characterization techniques, and together, we’ve been able to tackle some of the biggest challenges about this material.”
The paper, “Engineered Blended Thermoactivated Recycled Cement: A Study on Reactivity, Water Demand, Strength-Porosity, and CO2 Emissions,” was published December 27, 2024 in ACS Sustainable Chemistry & Engineering. In addition to Angulo and White, co-authors include Mateus Zanovello and Vanderley M. John of the University of São Paulo. The work is part of the National Institute on Advanced Eco-Efficient Cement-Based Technologies project, which is funded by Brazil’s National Council for Scientific and Technological Development (CNPq), the São Paulo Research Foundation (FAPESP), and the University of São Paulo. The work was also supported by the Carbon Mitigation Initiative at Princeton University, which is sponsored by bp and administered by the High Meadows Environmental Institute.